By 2020, global international aviation emissions are projected to be around 70% higher than in 2005 and the International Civil Aviation Organization (ICAO) forecasts that by 2050 they could grow by a further 300-700%1. Emissions from international aviation has increased substantially as a result of higher demand and consumption of jet kerosene, what also contributed to a 0.7% greenhouse gas emission in the EU in 20172. The Carbon Offsetting and Reduction Scheme for International Aviation, or CORSIA, aims to stabilize CO2 emissions at 2020 levels by requiring airlines to offset the growth of their emissions after 2020. Due to the fact, that by using graphene-based materials in composite aeronautical structures a weight reduction can be achieved, less fuel consumption will be realized3. It has been reported that 1 kg of mass reduction in an aircraft can save over 2900 liters of fuel per year1. This – on the long-term scale – contributes not only to the stabilization but also to the reduction of the CO2 emission levels.
The cost savings and all other impacts listed above (weight reduction, therefore CO2 emission reduction) can be deduced via two different aspects. Firstly, the replacement / partly replacement of steel parts in aerospace that leads to a massive weight reduction, and therefore fuel savings and reduced CO2 emission. So, firstly, these impacts will be realized by the utilization of the new innovative Ti6Al4V parts in the aircrafts. Benefits and Impact of Titanium use in aircraft engineering: Compared with conventional metallic materials (steel, aluminium) used in aeronautical engineering the utilization of titanium makes weight savings possible due to the specific strength advantage (thinner profiles can be realized). This may be true except for low alloyed ultrahigh strength steel (Steel 300M/S155), but here other (not only mechanical) advantages of titanium must be highlighted over steel: excellent corrosion resistance, no hydrogen embrittlement, high galvanic compatibility with standard toughened epoxy polymers (composite materials). As not only the strength, but also the stiffness is an important feature, one has to consider the specific E (Young’s) modulus, that remains, however essentially unchanged, when different parts are replaced by titanium.
Another key factor is the cost of titanium components for aerospace applications. Titanium has a cost disadvantage over steel due to its production process: titanium has to be obtained by reduction with Na or Mg in the so-called Kroll process using expensive chemicals, and labor-intensive multitude processes and due to necessary safety precautions. Additionally the buy to to fly ratio (BTF, that relates the mass of the raw material purchased, such as plate or billet, to the mass of the final machined component as in service, indication of the material lost during manufacture) is high for cast titanium. BTF is a factor of 5-7 for conventional produced titanium and can be as high as 40 depending on the complexity of the specific part geometry. Furthermore, the conventional machining is expensive (can be as high as 50% of total costs). However, innovative, new manufacturing technologies such as additive manufacturing are considered as a possibility of cost optimization of components, because there the buy-to-fly-ratio is close to 1 (there is nearly no waste) due to the near net shape process applied. This great advantage in BTF and the almost no machining costs outweigh the higher costs of titanium powder, which is produced by gas or plasma atomization. This is an unambiguous cost savings factor, regardless of the relatively higher costs of powder than mill products of forging stock (100-300 $/kg).
Weight savings can be realized, when replacing steel components of cargo doors: Cargo doors work on a complicated mechanism principle, and have many individual components that have to work precisely together: a malfunction of these metallic elements can lead to a crash, that provides not only a weight issue but also a safety issue4. According to the demands of 2019, projection of Airbus is that 39,210 aircrafts have to be built and delivered until the year 2038, 40% of which will be replacement and 60% completely new delivery5. Realization of 1 kg weight saving per cargo door when replacing steel parts by titanium will save therefore 39,210 kg weight, resulting in fuel saving of 93,242 tons of fuel/year. This saving in fuel is corresponding to a saving of CO2 emission of 293,710 tons/year, which would result in an overall reduction of the current total CO2 emission of global air travel by 0,03%. Besides these benefits, if these titanium parts are additively manufactured, regarding an average BTF ratio of 10 for conventional techniques, 45,700,000 $ cost savings are realizable (calculation is based on the actual titanium price on the market)110. Another interesting example for the benefit of AM processing is the replacement of the seat belt fixture by an AM processed Ti6Al4V part. Such a part could not be produced economically with conventional processing, only available with AM and brings additional weight gains by its intricate geometry, causing 85 grams of weight savings. This is for an Airbus A350-9000 with 325 seats an overall mass saving of 23.5 kg, equating to 0.16 % CO2 emission reduction of one airplane. The same applies among others for lattice structures, that could not be previously manufactured by traditional techniques, and of course, only to name one more example.
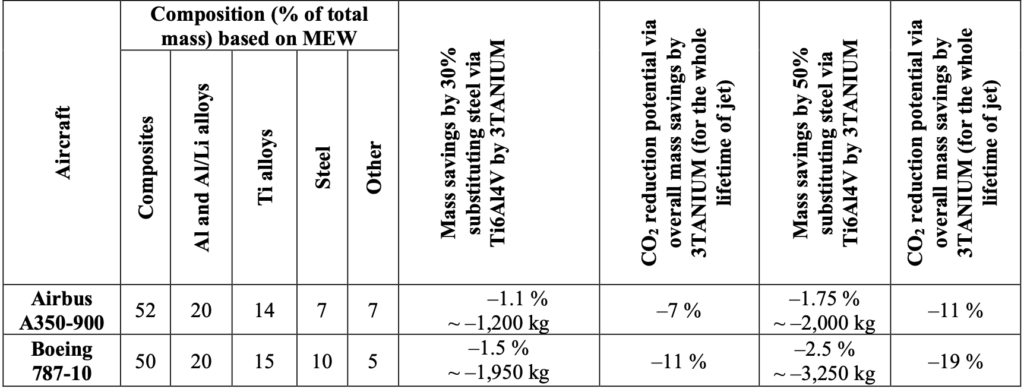
1 https://ec.europa.eu/clima/policies/transport/aviation_en
2 Annual European Union greenhouse gas inventory 1990–2017 and inventory report 2019
3 Soutis C. Carbon fibre reinforced plastics in aircraft construction. Materials Science and Engineering: A. 2005; 412(1-2): 171-176.
4 https://turkishdc10.wordpress.com/2008/01/05/ermenonville-memorial-location/
5 https://www.airbus.com/aircraft/market/global-market-forecast.html